Cold Forging
Through its 22 years of business and experience, EREZ has expanded its industry network and positioned itself in both domestic and international markets using the cold forging (shaping metal in a mold) method, a technique practiced by very few companies in Turkey. However, to become a leader in these markets, EREZ is tirelessly striving for excellence, focusing on both quality and significant advancements in production and R&D departments, aiming to provide quality to its customers at competitive prices and in a short timeframe.
22 Years of Experience Establishing a Presence in the Industry with Cold Forging Technology
With 22 years of experience and expertise, Erez has become a prominent industrial establishment in both domestic and international markets, employing the rare cold forging method. However, to achieve leadership goals, the company is taking significant strides in quality, production, and R&D areas.
Striving for Leadership in Quality, Production, and R&D
Erez is an industrial establishment dedicated to becoming a leader in the industry by prioritizing quality, production, and R&D efforts to provide customers with high-quality products at competitive costs and in a short time.
Cold Forging with High Tonnage Capacity Hydraulic and Mechanical Presses
Within the structure of EREZ , there are hydraulic and mechanical presses with tonnage capacities ranging from 250 tons to 1000 tons. Our facilities handle the cold shaping of parts ranging from 20 grams to 1500 grams. Utilizing the advantages of cold forging, we aim to offer customers high-quality production in a short time. By leveraging various technological programs, we continue our operations with the goal of providing efficient and quality production to our customers.
High-Capacity Hydraulic and Mechanical Presses
EREZ is an industry leader with hydraulic and mechanical presses ranging from 250 tons to 1000 tons, providing high-capacity machines designed to meet various industrial needs.
Fast and High-Quality Production with Cold Forging
Thanks to the cold forging production method, we provide customers with the advantage of fast delivery. We aim to meet the demands as soon as possible by optimizing our production processes with the speed and efficiency brought by cold forging technology.
Cold Forging Products
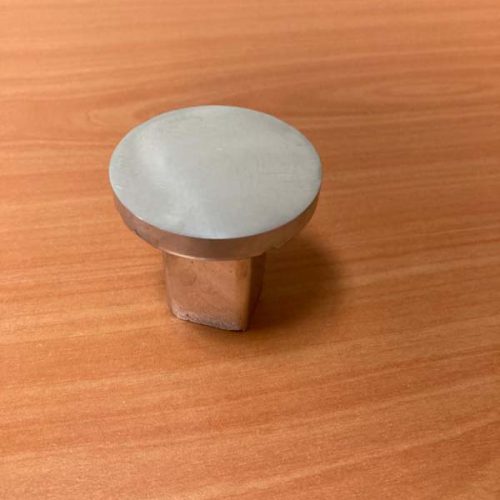
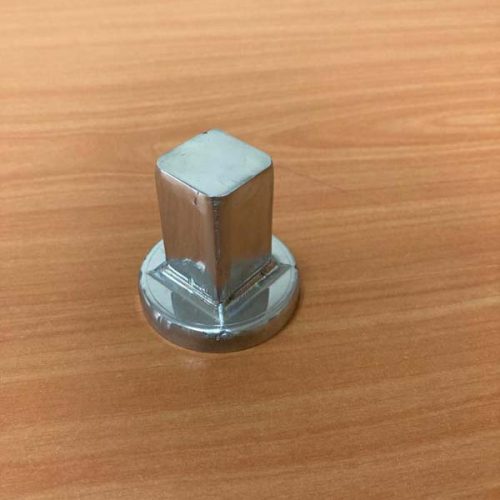
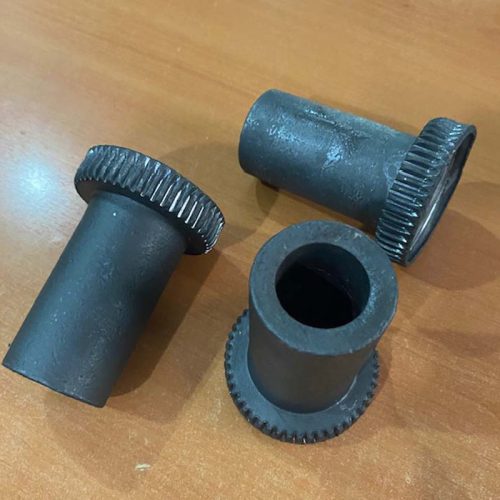
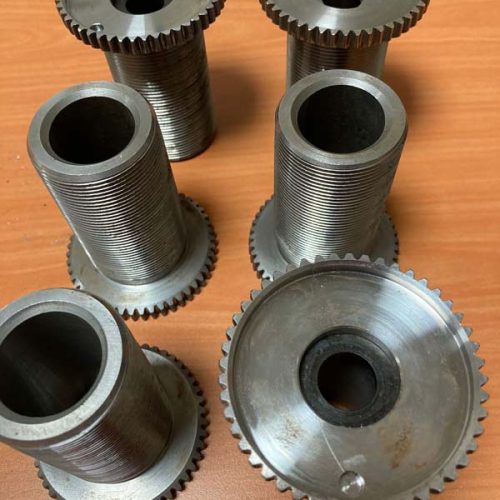
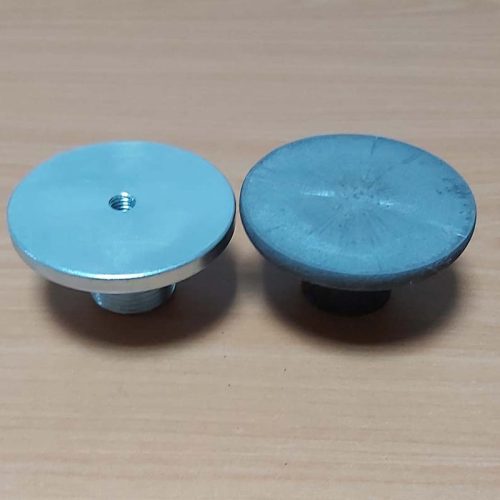
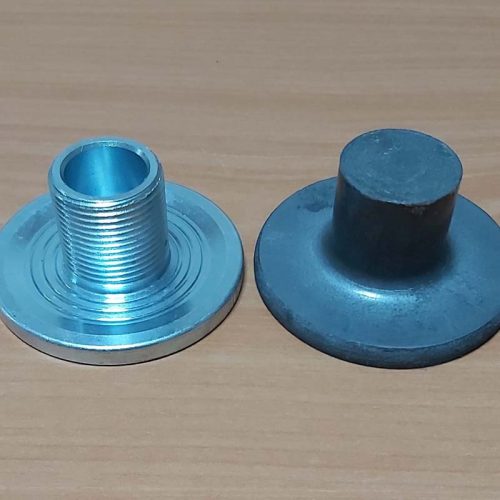
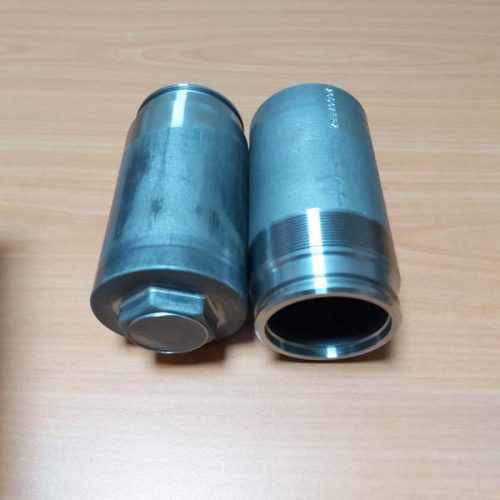
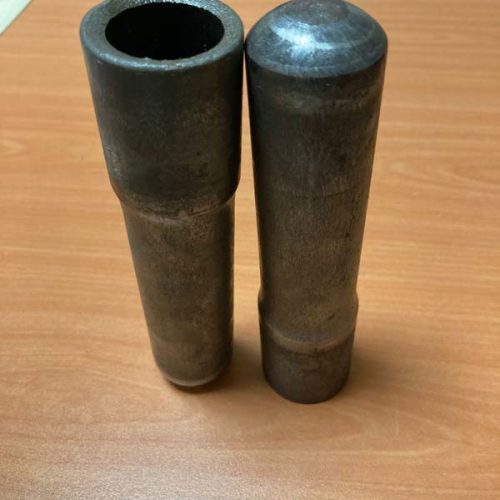
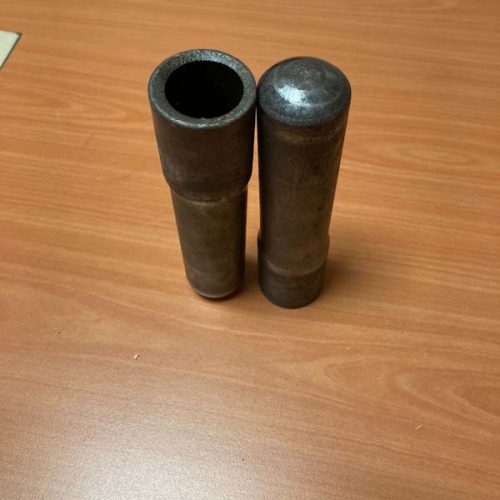
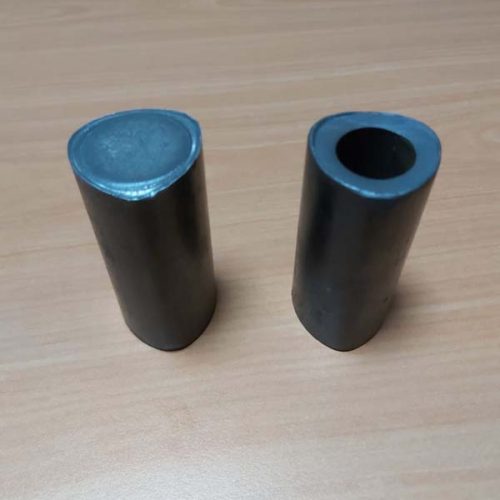
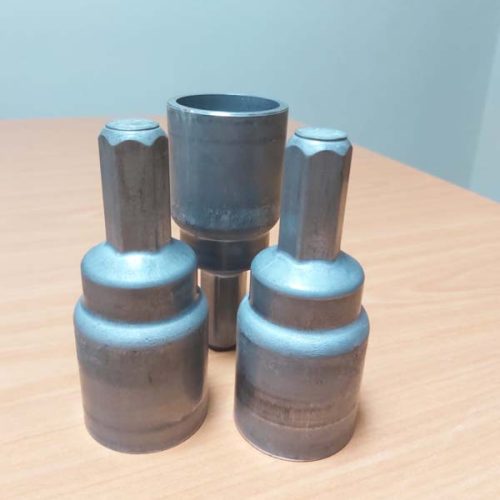

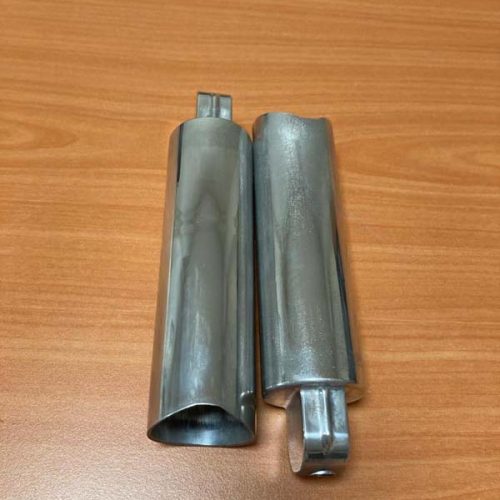
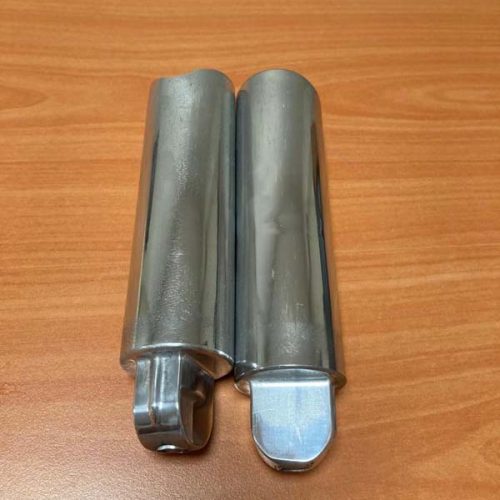
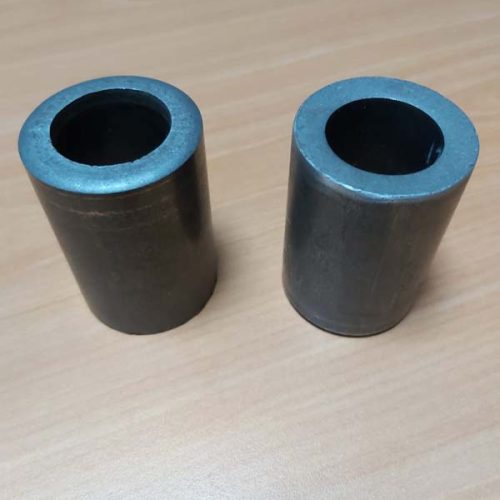
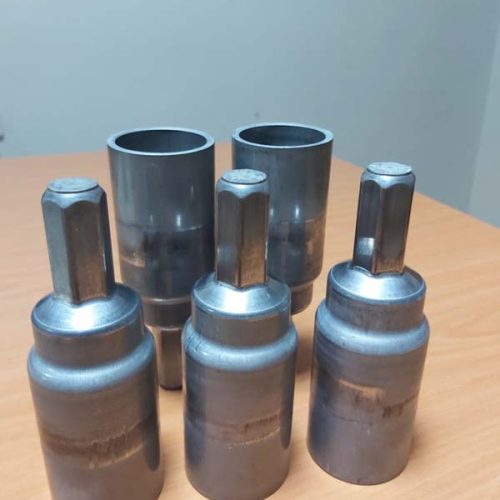
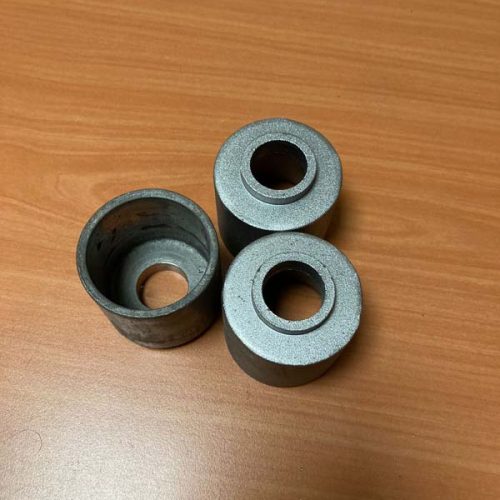
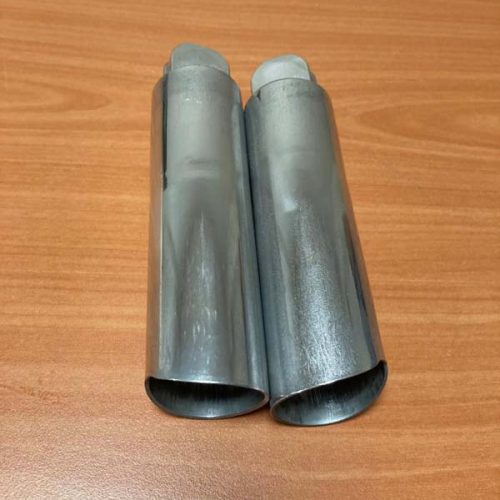
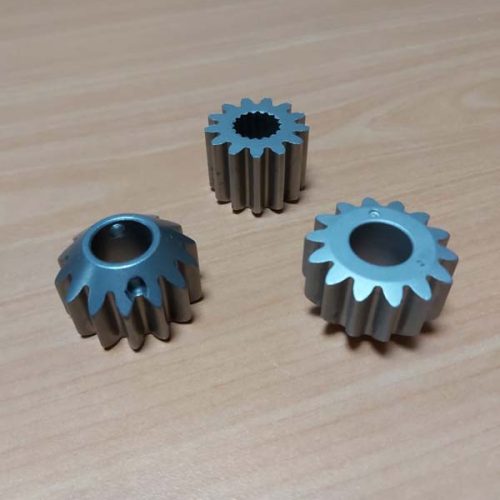
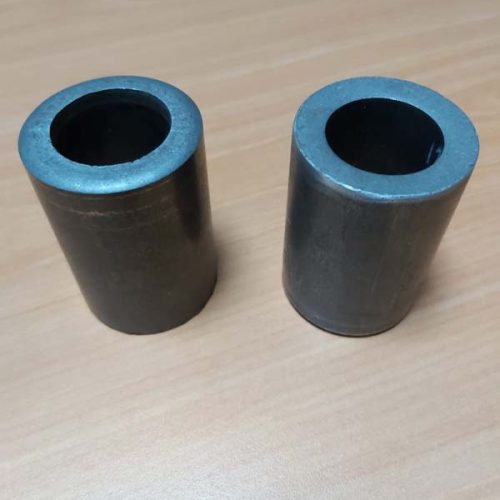
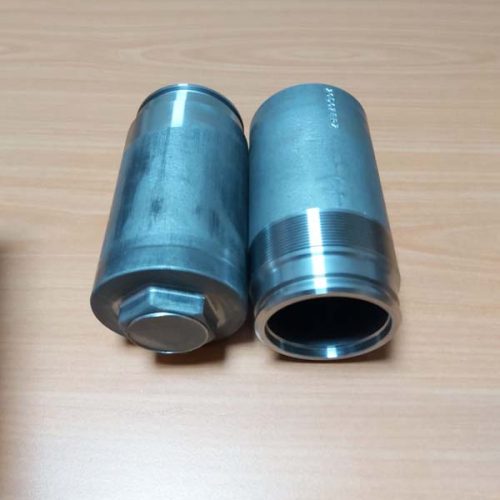
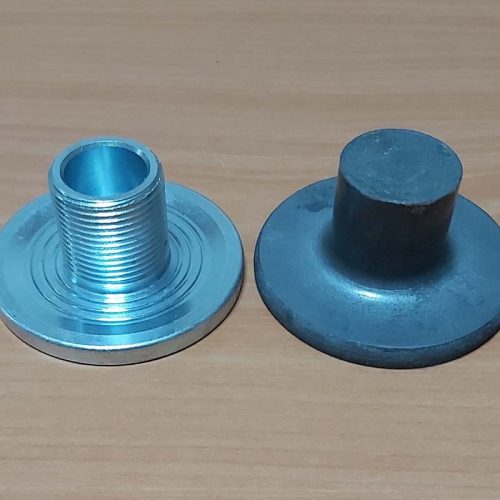
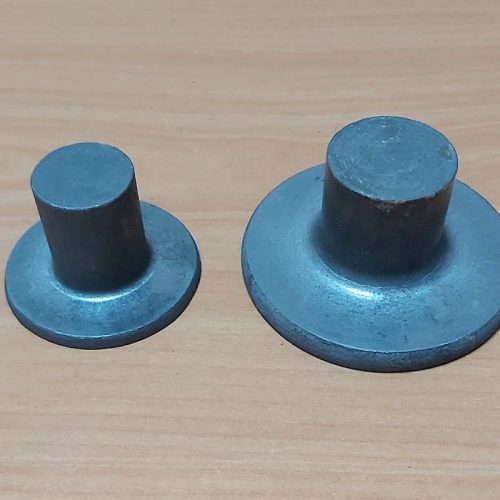
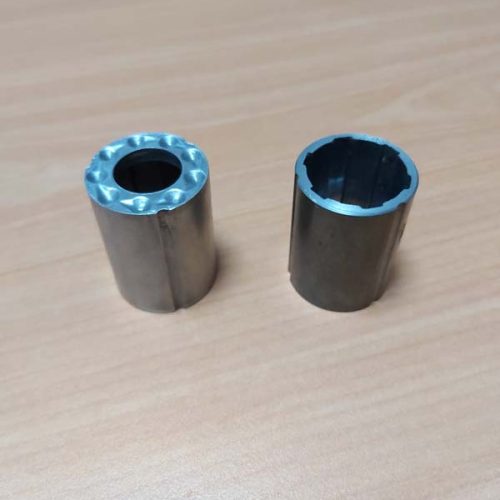
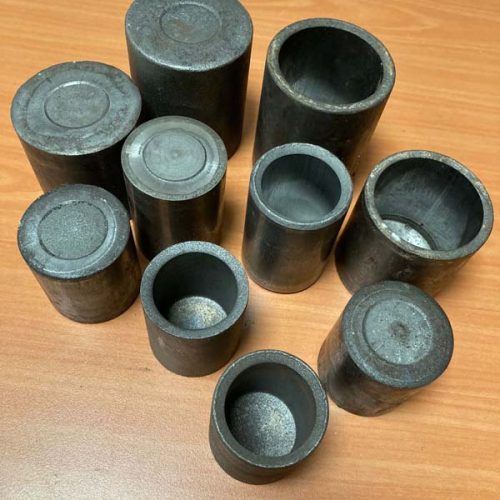
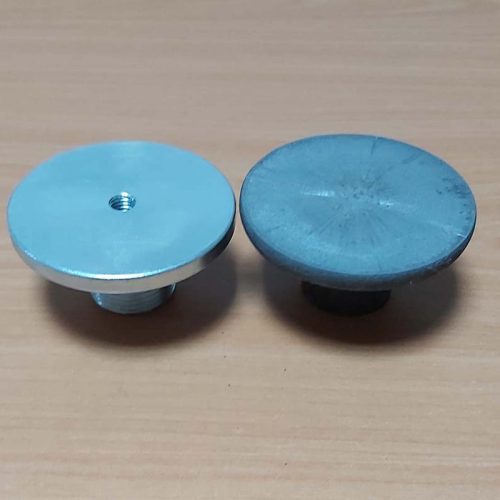

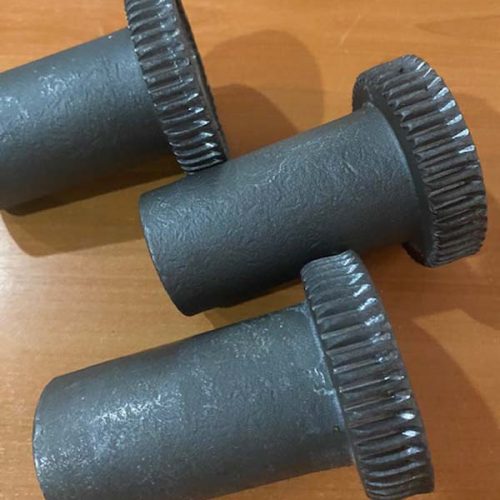
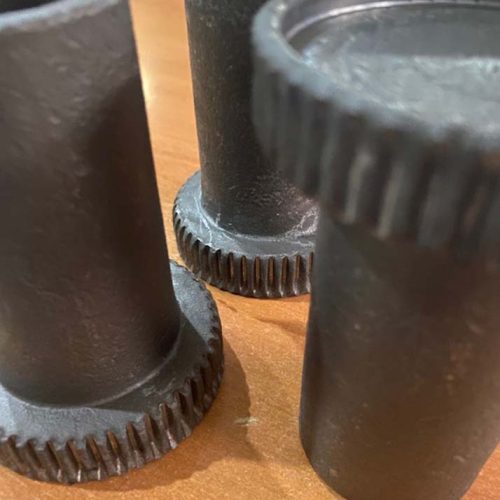
The Advantages of Cold Forging
Cold forging, which holds a significant place in modern manufacturing processes, offers various advantages. This method allows for the production of lighter and higher-quality products, leading to increased efficiency in manufacturing processes. Factors ranging from weight savings to profitability rates, advantages in production times, and hardness control contribute to the reasons for choosing cold forging. These advantages also result in fast delivery to customers and consistent quality standards.
Material Savings
Cold forging allows for reduced material usage compared to machining and hot forging in the production of the same part. While 1 kg of material is used for a part produced with chip machining, and the amount is between 800-900 grams for hot forging, the same part can be produced using cold forging with only 350-400 grams of material.
Low Heat Treatment
While 90-95% of parts obtained through chip machining and hot forging undergo heat treatment, this rate drops to 40-50% in cold forging. The ability to perform the forging process without compromising the grain structure of the part is a preferred feature, especially in the automotive sector.